Мартенситное превращение
Основная статья: Мартенситное превращение
Мартенситное превращение при охлаждении происходит не при постоянной температуре, а в определённом интервале температур, при этом превращение начинается не при температуре распада аустенита в равновесных условиях, а несколькими сотнями градусов ниже. Оканчивается превращение при температуре значительно ниже комнатной. Таким образом, в интервале температур мартенситного превращения в структуре стали, наряду с мартенситом, есть и остаточный аустенит.
При пластической деформации стали при температурах мартенситного превращения количество мартенсита увеличивается. В некоторых случаях также влияет упругая деформация. Возможно превращение аустенита в мартенсит при комнатных температурах под действием пластической деформации.
Кроме железоуглеродистых сплавов, мартенситное превращение наблюдается и в некоторых других, например, сплавах на основе титана (сплавы типа ВТ6, ВТ8, ВТ14), меди (бронзы типа БрАМц 9-3).
Мартенситные стали
К сталям мартенситного типа относят высоколегированные стали, структура которых после проведения термической обработки представлена мартенситом.
Сам по себе мартенситный сплав плохо поддается резанию. Его обрабатываемость повышают путем проведения предварительного отжига при температуре 800-900 ºC.
Как правило, мартенситные стали легируются такими металлами как вольфрам, никель и молибден для повышения жаропрочности и коррозионной устойчивости сплава к агрессивному воздействию среды.
Также мартенситная сталь обладает таким полезным свойством как самозакаливание, т. е. самопроизвольное повышение твердости после проведения термической обработки.
Стали мартенситного класса относятся к 3 группе свариваемости. Проведение сварки требует предварительного нагрева до 200-300 ºC и последующего отжига детали. Все это необходимо для снижения внутреннего напряжения и уменьшения вероятности образования трещин на поверхности сварного шва. На практике данные стали свариваются методом аргонодуговой и электрошлаковой сварки.
Механические свойства сталей на основе мартенсита достаточно высокие. Так, марка 15Х5, применяемая при изготовлении сосудов высокого давления, имеет предел прочности на разрыв равным почти 400 Мпа.
Дополнительное легирование вольфрамом и ванадием сильно повышает жаропрочность сплава. Предел прочности стали 10ХМФБ составляет уже 600 Мпа. Сталь нашла применение в производстве коллекторов, трубопроводов и нагревательных котлов.
Увеличение содержания бериллия в составе мартенситных сталей способствует дальнейшему повышению их механических свойств. Предел прочности стали 12Х11В2МФ равен примерно 850 Мпа. Такие марки применяются в производстве деталей, испытывающих повышенную тепловую и механическую нагрузку. Например, в корпусе и роторе газовой и паровой турбины, а также в качестве материала для лопаток турбовинтовых компрессоров.
Стали мартенситного класса достаточно упруги и хорошо сопротивляются ударным нагрузкам. Ударная вязкость колеблется в пределах 80-150 Дж\см2. Ее значение в большей степени зависит от типа термической обработки и содержания тех или иных элементов. Наибольшее ее значение получается в результате проведения закалки с последующим высоким отпуском.
Мартенситные стали не отличаются высоким значением пластичности. Относительное удельное сжатие равно 14-24%. Данный параметр зависит в большей степени от количества углерода в составе стали. Также такие элементы как никель и медь оказывают отрицательное влияние на пластичность сплава.
Рейтинг: /5 –
голосов
Что такое кристаллическая решетка
Как известно, все вещества состоят из частиц — атомов, которые могут располагаться хаотично или в определенном порядке. У аморфных веществ частицы расположены беспорядочно, а у кристаллических они образуют определенную структуру. Эта структура называется кристаллической решеткой. Она определяет такие характеристики вещества, как твердость, хрупкость, температура кипения и/или плавления, пластичность, растворимость, электропроводность и т. д.
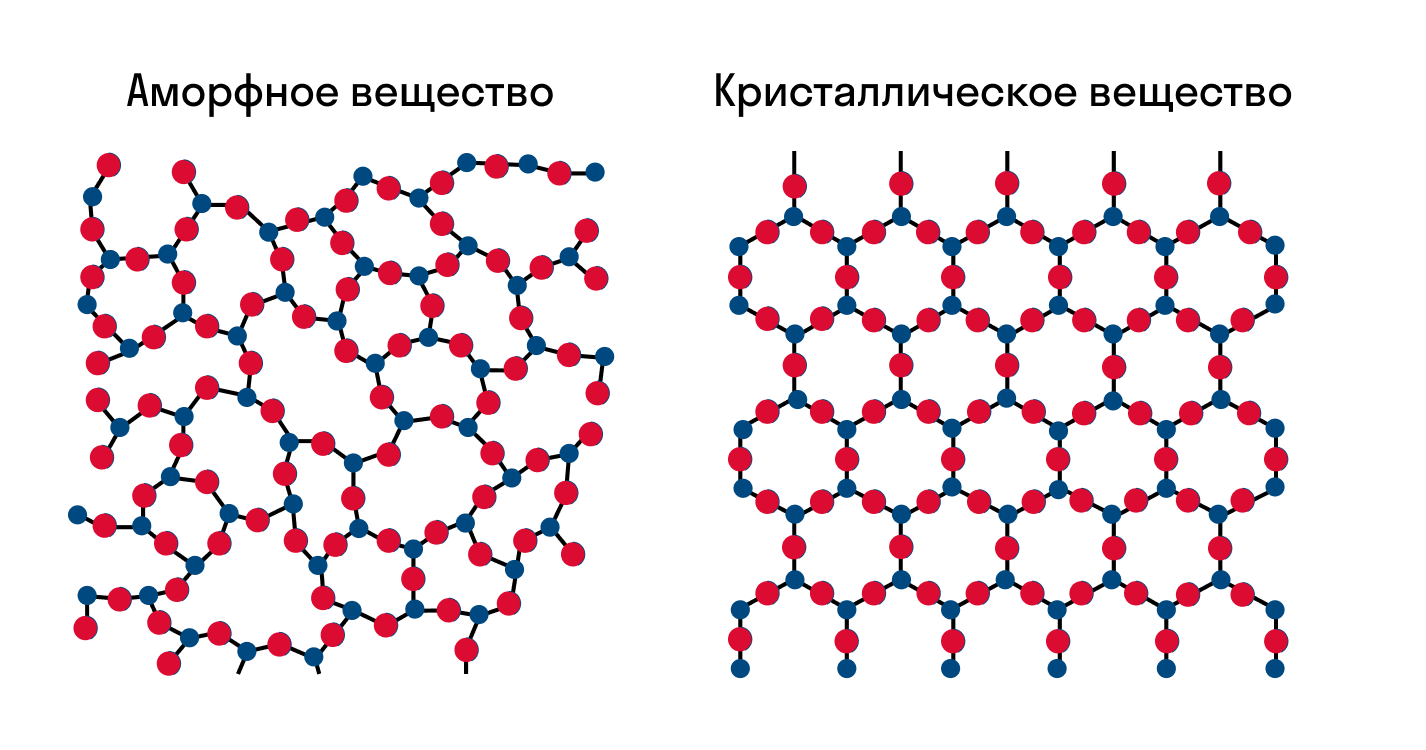
Кристаллическая решетка — это внутренняя структура кристалла, порядок взаимного расположения атомов, ионов или молекул. Точки, в которых находятся эти частицы, называются узлами решетки.
Частицы удерживаются на своих местах благодаря химическим связям между ними. В зависимости от того, какой вид связи удерживает атомы или ионы данного вещества, в химии выделяют основные типы кристаллических решеток:
атомная (ковалентные связи),
молекулярная (ковалентные связи и притяжение между молекулами),
металлическая (металлические связи),
ионная (ионные связи).
Важно!
Не путайте эти два понятия — кристаллическая решетка и химическая связь. Тип решетки говорит о том, как расположены атомы/ионы в молекуле вещества, а тип связи — по какому принципу они между собой взаимодействуют.
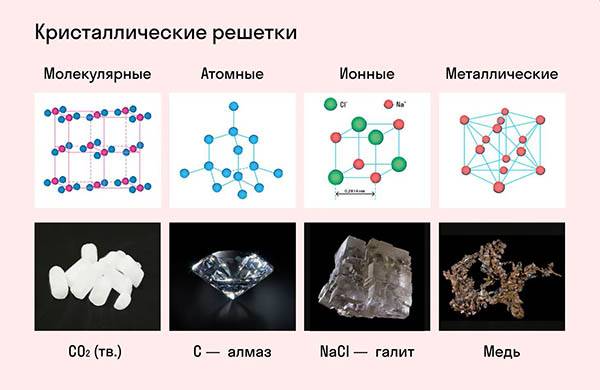
Практикующий детский психолог Екатерина Мурашова
Бесплатный курс для современных мам и пап от Екатерины Мурашовой. Запишитесь и участвуйте в розыгрыше 8 уроков
Получить
Применение мартенситных марок стали
В мартенситные стали добавляют легирующие элементы, чтобы получить нужные свойства сплавов: прочность, износостойкость, хладо-жаропрочность, коррозийную стойкость. В одной марке легированной стали может быть до 7 легирующих элементов. Стали легируют никелем, хромом, азотом, вольфрамом, бериллием, ванадием, кремнием, молибденом, медью, бором.
Обычно в обозначении стали зашифрованы легирующие добавки и их количество (38ХН3МФА), некоторые экспериментальные шифруются буквой Э. В этом случае буква не отражает состава стали – ЭИ, ЭП3. Иногда стали, предназначенные для изготовления выпускных авиационных и автомобильных клапанов, называют сокращенно – сильхромы.
Легированные мартенситные стали способны противостоять агрессивным среда: кислотам, щелочам, солям, агрессивным газам. По применению мартенситные стали бывают коррозионностойкие, жаростойкие, жаропрочные и стали специального назначения.
Коррозионностойкие марки сталей (15Х28, 20Х13, 12Х18Н9) применяют на опытных производствах, в химической промышленности.
Жаростойкие марки сталей (ХН60Ю, 12Х25Н16Г7АР, (15Х6СЮ) используют для изготовления деталей, которые работают под умеренной нагрузкой при температурах до 1000 градусов.
Изделия из жаропрочных марок сталей (15Х6СЮ, 08Х13, 14Х17Н2) могут работать под нагрузкой весьма длительный и длительный период при высоких температурах.
К специальным сталям можно отнести стали, из которых катают броневой сэндвич. Отдельное место занимает сталь Гадфильда (1,1% углерода, 13% магния). При работе в условиях высоких давлений происходит самопроизвольная пластическая деформация и соответственно увеличивается степень ее прочности. Уникальные механические свойства пока не до конца изучены.
Магнитные свойства мартенситной стали
У мартенситной структуры кристаллической решетки стали ярко выражены магнитные свойства. Мартенсит – ферромагнетик в чистом виде. Однако выдержать идеальный химический состав сложно. Углеродистые мартенситные стали, легированные молибденом, кобальтом и хромом (ЕХ9К15М2), кобальтом и хромом (ЕХ5К6), хромом (ЕХ3) можно отнести магнитотвердыми материалами.
Легирование кобальтом наиболее эффективно с точки зрения магнетизма – у атомов кобальта присутствует магнитный момент, таким образом, остаточная индукция мартенсита возрастает. Низкая цена и легкость механической и термической обработки дает возможность применения мартенситных сталей в магнитных системах в качестве переключателей для изменения направления при подаче управляющих сигналов.
Свариваемость мартенситных сталей
Технологии сварки мартенситных сплавов усложняются повышенной хрупкостью металла после закалки. Эти типы стали варят после предварительного нагрева примерно от 200 до 450 градусов, температура окружающей среды не должна быть отрицательной. Обычно детали из стали мартенситной группы сваривают методами ручной дуговой сварки электродами, покрытыми специальными составами. Иногда используют и другие виды сварки: аргонодуговые, электрошлаковые, под флюсом.
Структура мартенсита
Основным отличием, которое приводит к изменению физических и механических характеристик стали является изменение внутренней структуры. Её называют мартенситная структура. В этом случае кристаллическая решётка претерпевает следующие изменения. Под воздействием внешних факторов происходит изменение направления движения атомов по сравнению с их стандартным, упорядоченным движением в рамках установленной решётки. Увеличиваются межатомные расстояния, что приводит к возникновению деформации, примерно на 10% относительно нормальных размеров. Величина изменений не приводит к переходу через энергетический барьер межатомных связей. Такой кристаллический эффект приводит к образованию специфической формы взаимных связей. Она носит так называемый игольчатый характер.
Изменения структуры стали происходит в процессе нагрева. Повышение температуры вызывает диффузионное перераспределение атомов углерода в рамках кристаллической решётки. Этот процесс вызывает образование нескольких фаз металла.
- При повышении содержания углерода до 6,7% возникает материал называемый цементит. Он имеет решётку в форме ромба.
- При низком содержании углерода (не более 0,02%) формируется феррит. Его решётка приобретает объёмно-центрированную форму.
- Аустенит. Структура железоуглеродистых сплавов, представляющих смесь углерода в количестве около 2% различных легирующих добавок. Кристаллическая решётка этого материала имеет форму куба со строго центрированными гранями. Отличительной особенностью аустенита является его высокая плотность по сравнению с другими структурами стали. Он образуется при температуре нагрева от 910 до 1401 °С и сохраняет свою устойчивость до температуры 723 °С. При дальнейшем охлаждении превращается в другие более устойчивые структуры. При добавлении никеля, марганца или хрома аустенит сохраняет свою структуру вплоть до комнатной температуры. К сталям, имеющим аустенитную структуру, относятся почти все хромоникелевые стали.
- Перлит является механической смесью цементита и феррита. В этой смеси присутствие углерода составляет 0,8%. Он образуется из аустенита в процессе охлаждения. Он является эвтектоидом и может обладать пластичной или зернистой структурой. От этого состояния зависят его физические и особенно механические свойства.
- При повышении содержания углерода до 4,3% из смеси аустенита и цементита образуется материал, называемый ледебурит. Его формирование происходит при температуре расплава в 1147 °С.
- Мартенсит – это перенасыщенный раствор железа и углерода. Его обычно получают при закалке аустенита. В результате температурного воздействия мартенситный материал приобретает из кубической тетрагональную решётку, которая придаёт ему твердость до 1000 HV.
В результате обработки полученная мартенситная сталь приобретает игольчатую структуру, которая формирует более высокие прочностные характеристики, становится устойчивее к воздействию коррозии
Мартенситные точки
Основной характеристикой сплавов при определенном режиме закалке является мартенситные точки.
Температура начала мартенситных превращений обозначается Мн. При достижении температуры охлаждения стали значений Мн начинается мгновенный лавинообразный процесс перекристаллизации стали. Температура Мн определяется для каждой марки стали экспериментальным путем на металлургических предприятиях. Значение Мн снижается от увеличения количества углерода и легирующих элементов в составе стали.
Температура конца мартенситных превращений обозначается Мк. В промежутке значений температур между Мн и Мк происходит бездиффузная перестройка кристаллической решетки стали. При достижении температуры Мк бездиффузная перекристаллизация прекращается. Для высокоуглеродистых легированных сталей она может быть отрицательной.
Практика термической обработки сталей на мартенсит
На крупносерийных и массовых производствах для закалки стальных изделий используют автоматические конвейерные линии, на которых производится полный цикл получения необходимой мартенситной структуры для определенных марок стали.
В инструментальных цехах и на опытных производствах инструмент и детали закаляют вручную путем нагрева инструмента в муфельных печах, в ваннах с маслами, солями или расплавленными металлами. Охлаждение производится в разных средах: воде, масле, воздухе. Параметры температур и процесса закалки разрабатывает технолог согласно техническим нормам и марочникам стали.
Поверхностный нагрев осуществляют в тех случаях, когда нужно повысить прочность наружных слоев изделий при сохранении мягкой сердцевины. Поверхностная закалка производится в генераторах высокой частоты.
В зависимости от требуемой температуры нагрева применяют различные соли или смеси солей; так при высокотемпературных нагревах (1000-1300 градусов), используют расплавленный хлористый барий, при нагревах до 750-950 градусов используют смеси солей хлористого бария, хлористого калия и хлористого натрия. При низкотемпературных нагревах 300-550 градусов используют смеси калиевой и натриевой селитр.
В качестве охлаждающих сред при закалке на мартенсит чаще всего применяют жидкие среды различной охлаждающей способности. Обычно используют воду, а скорость отвода теплоты увеличивают добавлением едкого натра. К более мягким охладителям относятся масла – минеральные и трансформаторные.
Виды закалки на мартенсит
- Непрерывная, или закалка в одной среде.
- Закалка в двух средах.
- Ступенчатая закалка.
- Обработка холодом.
После нагревания стального изделия до температуры аустенитной фракции, его резко охлаждают либо в воде (самый простой вариант), либо в подогретых маслах, либо на воздухе в зависимости от состава стали. При таком способе охлаждения появляются коробления, а иногда и трещины.
Во избежание рисков используют закалку в двух средах. После нагрева изделие погружают в воду, некоторое время выдерживается, и затем дальнейшее охлаждение до температуры до Мк происходит в более мягкой среде. Этот способ походит для серийных производств.
При ступенчатой схеме охлаждения, сталь, погружают в охлаждающую жидкость, с температурой, превышающей Мп на 60-100 градусов, выдерживают расчетное время, и в дальнейшем охлаждают на спокойном воздухе. Такому виду охлаждения подвергают малогабаритный инструмент из средне- и низколегированных сталей.
К охлаждению в холоде (жидком азоте) обычно прибегают в случаях, когда Мк для марки стали оказывается ниже нуля. Это высоколегированные углеродистые марки, используемые для изготовления мерительного инструмента и элементов подшипников качения.
Металлическая кристаллическая решетка
Для начала вспомним, как проходит металлическая химическая связь. В молекуле металла свободные отрицательно заряженные электроны перемещаются от одного иона к другому и соединяются с некоторыми из них, а после отрываются и мигрируют дальше. В результате получается кристалл, в котором ионы превращаются в атомы и наоборот.
Металлическая кристаллическая решетка — это структура, которая состоит из ионов и атомов металла, а между ними свободно передвигаются электроны. Как несложно догадаться, она характерна лишь для металлов и сплавов.
Свободные электроны, мигрирующие между узлами решетки, образуют электронное облако, которое под воздействием электротока приходит в направленное движение. Это объясняет такое свойство металлов, как электрическая проводимость.
В химии типичным примером вещества, которое имеет металлическую кристаллическую решетку, считается медь. Она очень ковкая, пластичная, имеет высокую тепло- и электропроводность. Впрочем, все металлы ярко демонстрируют эти характеристики, поэтому назвать физические свойства данной группы несложно.
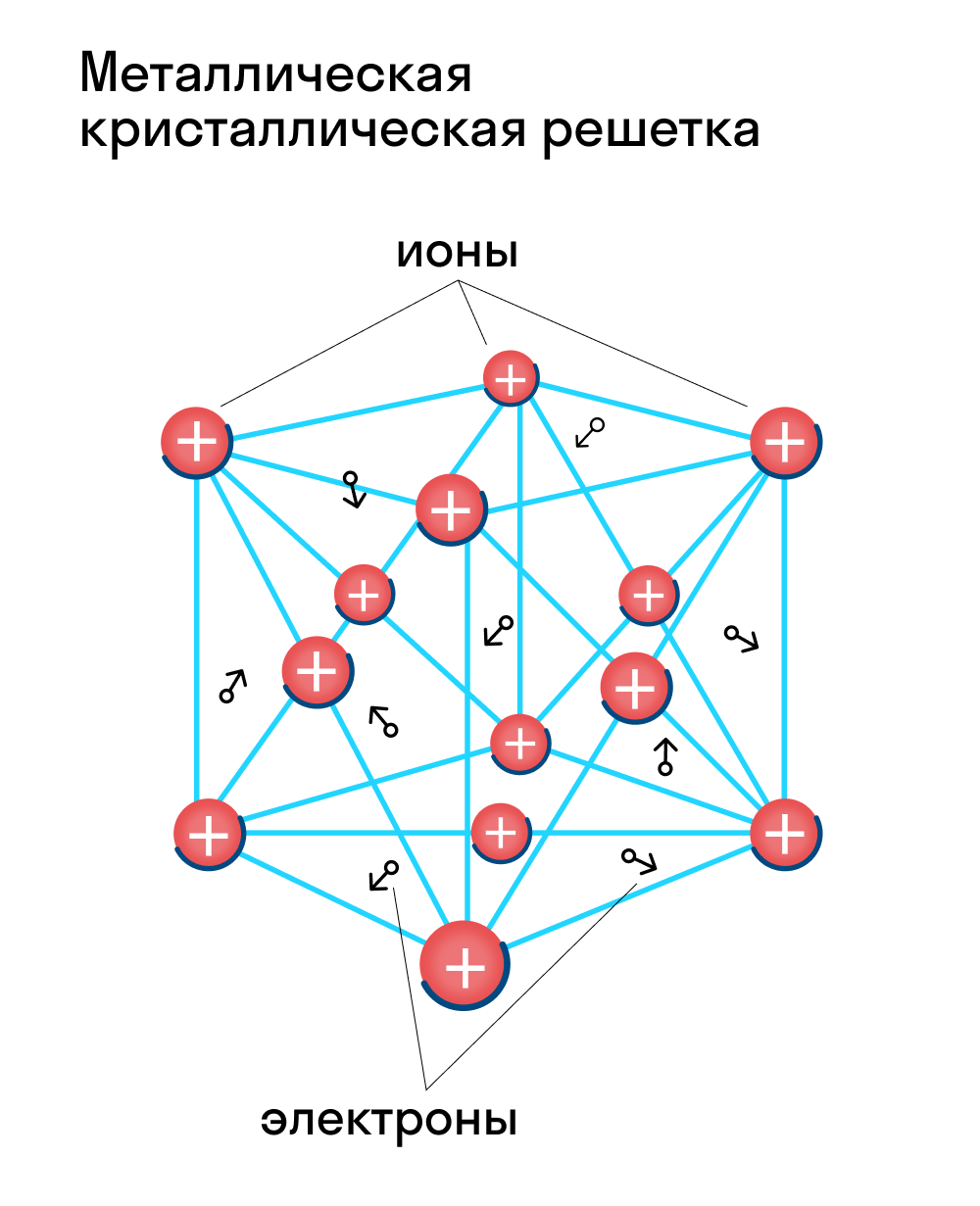
Свойства веществ с металлической кристаллической решеткой:
характерный блеск;
хорошая ковкость;
высокая теплопроводность;
электропроводность.
При этом температура плавления веществ может существенно различаться. Например, у ртути это −38,9°С, а у бериллия целых +1287°С.
Особенности образования
Аустенит – это структура, которая формируется в процессе нагревания стали. При достижении критической температуры перлит и феррит образуют целостное вещество.
Варианты нагревания:
- Равномерное, до достижения необходимого значения, непродолжительная выдержка, охлаждение. В зависимости от характеристик сплава, аустенит может быть как полностью сформирован, так и частично.
- Медленное повышение температуры, длительный период поддержания достигнутого уровня теплоты с целью получения чистого аустенита.
Свойства полученного разогретого материала, а также того, который будет иметь место в результате охлаждения. Очень многое зависит от уровня достигнутого тепла
Важно не допустить перегрев или перепал
Мартенситная сталь
Мартенситные стали, имеющие характеристики между аустенитными и легированными никелем сталями, структурные отвердения, могут быть использованы в криогенной технике, в частности сталь KS1140, механические характеристики которой приведены в нижеследующей таблице.
Мартенситные стали, содержащие 12 — 13 % Сг, появились на широком рынке в 1912 — 1915 гг. в виде ножевых изделий, а первым, кто ясно представил их промышленные возможности, был X. В результате его очень часто называют изобретателем нержавеющей стали. В действительности же целый ряд исследований этих сплавов был выполнен еще в предшествующем десятилетии. Например, Гулле в 1902 — 1906 гг. и Портевен в 1909 — 1911 гг. во Франции и Гисен в 1907 — 1909 гг. в Англии изучали металлургию и физические свойства таких сталей.
Мартенситные стали, содержащие 13 % Сг, не предназначены для применения в морской воде. Напротив, использование стали 431S29 и дисперсионно твердеющих сортов в некоторых случаях оказалось успешным, однако следует учитывать, что в определенных условиях и эти стали подвержены коррозии. Те же оговорки относятся и к ферритным сталям, но на практике они редко применяются в условиях контакта с морской водой.
Зависимость скорости коррозии различ. |
Мартенситные стали подвержены коррозионному растрескиванию только в состоянии высокой прочности.
Мартенситные стали свариваются высоколегированными хромо-никелевыми электродами, дающими наплавленный металл с высокой пластичностью. За счет пластичности наплавленного металла снижаются внутренние напряжения в сварном шве.
Мартенситные стали имеют оптимальную коррозионную стойкость после закалки из аустенитной области. В этом состоянии они обладают большой твердостью и хрупкостью.
Мартенситные стали, например 15Х11МФ, 15Х12ВНМФ, 10Х12НЗД, 18Х11МНФБ, 10Х12НД, предназначены для работы при температуре до 650 С. Из них делают, например, лопатки и диски паровых турбин и газотурбинных установок. Их дополнительно легируют молибденом, вольфрамом, ниобием, ванадием и никелем ( до 3 2 %), повышающими сопротивление сталей ползучести под напряжением при высокой температуре.
Мартенситные стали после отжига удовлетворительно обрабатываются резанием, горячая обработка давлением и сварка этих сталей затруднены из-за образования мартенсита.
Мартенситные стали предназначены для изделий, работающих при 450 — 600 С; от перлитных они отличаются повышенной стойкостью к окислению в атмосфере пара или топочных газов. По своей жаропрочности эти стали немного превосходят перлитные.
Мартенситные стали, если их подвергнуть термической обработке для повышения твердости, приобретают сильную склонность к растрескиванию в слабо — и умереннокислых растворах. Особенно это проявляется в присутствии сульфидов, соединений мышьяка или продуктов окисления фосфора или селена. Специфические свойства кислот не имеют существенного значения до тех пор, пока процесс идет с выделением водорода. Эта ситуация отличается от случая аустенитных сталей, которые разрушаются исключительно в результате специфического действия анионов. Катодная поляризация также не защищает мартенситные стали от растрескивания, а ускоряет его. Все эти факты свидетельствуют, что мартенситные стали в указанных условиях разрушаются не по механизму КРН, а в результате водородного растрескивания ( см. разд. При катодной поляризации в морской воде, особенно при высоких плотностях тока, более пластичные ферритные стали подвергаются водородному вспучиванию, а не растрескиванию. Аустенитные нержавеющие стали устойчивы и к водородному вспучиванию, и к водородному растрескиванию.
Мартенситные стали типа 17X15НЗМ и 15Х16Н2М используются в качестве теплостойких при температурах до 500 С.
Феррито-мартенситные и мартенситные стали имеют сравнительно с ферритными сталями пониженные кислотостойкость и окалиностой-кость и повышенну-ю прочность.
Химический состав ( в процентах и магнитные свойства мартенситных сталей для постоянных магнитов. |
Поскольку мартенситные стали являются почти единственной группой магнитотвердых материалов, поставляемых не в виде готовых магнитов или заготовок, а в виде прутков разного сортамента, и операции по изготовлению магнитов, включая, как правило, термообработку, выполняются потребителем, следует подчеркнуть необходимость тщательного соблюдения режимов термообработки для получения оптимальных магнитных свойств.
Мартенситные точки
Основной характеристикой сплавов при определенном режиме закалке является мартенситные точки.
Температура начала мартенситных превращений обозначается Мн. При достижении температуры охлаждения стали значений Мн начинается мгновенный лавинообразный процесс перекристаллизации стали. Температура Мн определяется для каждой марки стали экспериментальным путем на металлургических предприятиях. Значение Мн снижается от увеличения количества углерода и легирующих элементов в составе стали.
Температура конца мартенситных превращений обозначается Мк. В промежутке значений температур между Мн и Мк происходит бездиффузная перестройка кристаллической решетки стали. При достижении температуры Мк бездиффузная перекристаллизация прекращается. Для высокоуглеродистых легированных сталей она может быть отрицательной.
Практика термической обработки сталей на мартенсит
На крупносерийных и массовых производствах для закалки стальных изделий используют автоматические конвейерные линии, на которых производится полный цикл получения необходимой мартенситной структуры для определенных марок стали.
В инструментальных цехах и на опытных производствах инструмент и детали закаляют вручную путем нагрева инструмента в муфельных печах, в ваннах с маслами, солями или расплавленными металлами. Охлаждение производится в разных средах: воде, масле, воздухе. Параметры температур и процесса закалки разрабатывает технолог согласно техническим нормам и марочникам стали.
Поверхностный нагрев осуществляют в тех случаях, когда нужно повысить прочность наружных слоев изделий при сохранении мягкой сердцевины. Поверхностная закалка производится в генераторах высокой частоты.
В зависимости от требуемой температуры нагрева применяют различные соли или смеси солей; так при высокотемпературных нагревах (1000-1300 градусов), используют расплавленный хлористый барий, при нагревах до 750-950 градусов используют смеси солей хлористого бария, хлористого калия и хлористого натрия. При низкотемпературных нагревах 300-550 градусов используют смеси калиевой и натриевой селитр.
В качестве охлаждающих сред при закалке на мартенсит чаще всего применяют жидкие среды различной охлаждающей способности. Обычно используют воду, а скорость отвода теплоты увеличивают добавлением едкого натра. К более мягким охладителям относятся масла – минеральные и трансформаторные.
Виды закалки на мартенсит
- Непрерывная, или закалка в одной среде.
- Закалка в двух средах.
- Ступенчатая закалка.
- Обработка холодом.
После нагревания стального изделия до температуры аустенитной фракции, его резко охлаждают либо в воде (самый простой вариант), либо в подогретых маслах, либо на воздухе в зависимости от состава стали. При таком способе охлаждения появляются коробления, а иногда и трещины.
Во избежание рисков используют закалку в двух средах. После нагрева изделие погружают в воду, некоторое время выдерживается, и затем дальнейшее охлаждение до температуры до Мк происходит в более мягкой среде. Этот способ походит для серийных производств.
При ступенчатой схеме охлаждения, сталь, погружают в охлаждающую жидкость, с температурой, превышающей Мп на 60-100 градусов, выдерживают расчетное время, и в дальнейшем охлаждают на спокойном воздухе. Такому виду охлаждения подвергают малогабаритный инструмент из средне- и низколегированных сталей.
К охлаждению в холоде (жидком азоте) обычно прибегают в случаях, когда Мк для марки стали оказывается ниже нуля. Это высоколегированные углеродистые марки, используемые для изготовления мерительного инструмента и элементов подшипников качения.